Physical and Electrical Specs
Sheath Diameter +-0.005" (+-0.13mm) |
0.260" (6.60mm) |
0.315" (8.00mm) |
0.375" (9.52mm) |
0.430" (10.92mm) |
0.475" (12.07mm) |
0.496" (12.60mm) |
Sheath Length Max. |
404" (10,260mm) |
370" (9398mm) |
337" (8560mm) |
329" (8356mm) |
281" (7137mm) |
263" (6680mm) |
Maximum Voltage |
250 |
480 |
480 |
600 |
600 |
600 |
Maximum Amperage |
15 |
30 |
30 |
40 |
40 |
40 |
Wattage Tolerance |
Industry Standard +5% -10% |
Resistance Tolerance |
Industry Standard +10% -5% |
Length
Overall Sheath Length |
11-20" |
21-50" |
51-80" |
81-110" |
111-140" |
141-170" |
171-200" |
201"& up |
Sheath Length |
± 3/32" |
± 1/8" |
± 5/32" |
± 3/16" |
± 7/32" |
± 1/4" |
± 3/8" |
± 1/2" |
Heated Length |
± 1/4" |
± 1/2" |
7/8" |
± 1 1/8" |
± 1 3/8" |
± 1 5/8" |
± 1 7/8" |
± 2 3/8" |
Minimum Unheated |
1" |
1 1/4" |
1 1/2" |
1 5/8" |
1 3/4" |
2" |
2 1/4" |
2 1/2" |
Tubular Sheath, Temperature and Watt Density Guidelines
Heated Medium |
Process Temperature
°F (°C) |
Sheath Material |
Max. Watt Density
W/in2 (W/cm2) |
SOLIDS |
Clamp on to Metal |
To 500 (260)
To 1000 (540) |
Incoloy® |
20 (3)
10 (1.5) |
Milled Groove Molds |
To 500 (260)
To 1000 (540) |
Incoloy® |
60 (9)
30 (4.5) |
Vacuum Platens |
To 650 (345)
To 1000 (540) |
Aluminum, SS
Incoloy® or Inconel® |
40 (6)
20 (3) |
LIQUIDS |
Clean Potable Water |
To 212 (100)
To 500 (260) |
Copper
Incoloy® |
60 - 90 (9 - 14)
30 - 40 (4.5 - 6) |
De-I Water |
To 212 (100) |
316SS |
60 (9) |
Process Water &
Very Diluted Corrosives |
To 200 (95) |
304SS or Incoloy® |
48 (7.5) |
Mild or Diluted Acids &
Alkalies |
To 200 (95) |
Incoloy®, 316SS or
Inconel® |
15-23 (2.3 - 3.5) |
Oils (Depends on Type & Use) |
50 - 600 (10-315) |
Steel 6 - 23 |
(1 - 3.5) |
AIR |
Ovens, Natural Convection |
To 700 (370)
To 1200 (650) |
Incoloy® |
30 (4.5)
10 (2.3) |
Flowing Air @
Min. 500 fpm |
To 800 (425)
To 1000 (650) |
Incoloy® |
30 (4.5)
23 (3.5) |
Available Sheath Materials and Maximum Recommended Sheath Temperatures
Sheath Materials |
Maximum Temperature in Air °F (°C) |
Typical Applications |
Standard Available Sheath Materials |
Copper |
350 (175) |
Clean, potable water heating |
Aluminum |
750 (400) |
Vacuum platens |
Steel |
750 (400) |
Oils, glycol, molten salts, non-corrosives |
304SS |
1200 (650) |
Improved corrosion resistance over steel |
316SS |
1200 (650) |
De-ionized water and some corrosives |
Incoloy® 840 |
1600 (870) |
Improved corrosion resistance over steel and 304SS |
Incoloy® 800 |
1600 (870) |
Improved resistance to chloride attack, other corrosives |
Other Available Sheath Materials |
321SS |
1200 (650) |
Improved corrosion resistance over steel and 304SS |
Incoloy® 825 |
1600 (870) |
Highly resistant to many acids, salts, and other media |
Inconel® 600 |
1800 (980) |
Highly resistant to many acids, salts, and other media |
Heater Mounting Options
TYPE R MOUNTING - Locator washers
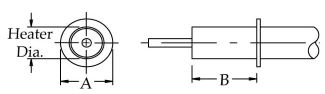
Heater Diameter |
A |
B |
0.260" |
3/4" |
Specify |
0.315" |
5/8" |
Specify |
0.375" |
3/4" |
Specify |
0.430" |
3/4" |
Specify |
0.475" |
3/4" |
Specify |
TYPE K MOUNTING - Mounting bracket
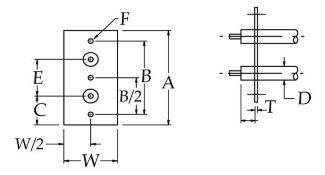
Specify all required dimensions and tolerances.
TYPE F MOUNTING - Mounting flange
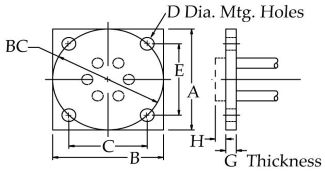
Specify all required dimensions and tolerances.
TYPE B MOUNTING - Threaded bulkhead fittings
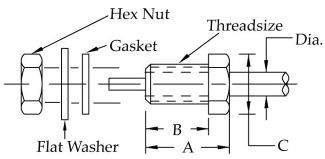
Type |
Material |
BB |
Brass |
BS |
Steel |
B4 |
304SS |
Diameter |
Thread |
A |
B |
C |
0.260" |
1/2 - 20 |
3/4" |
5/8" |
3/4" |
0.315" |
1/2 - 20 |
3/4" |
5/8" |
3/4" |
0.375" |
5/8 - 18 |
15/16" |
3/4" |
7/8" |
0.430" |
5/8 - 18 |
15/16" |
3/4" |
7/8" |
0.475" |
3/4 - 20 |
1" |
7/8" |
1" |
Tubular Heater Termination Options
TYPE S TERMINATION - Threaded stud terminal with a ceramic insulator.
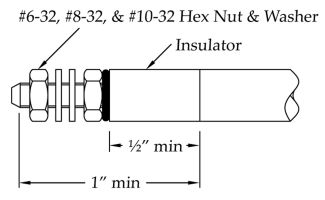
TYPE S1 TERMINATION - Threaded stud terminal with stacked mica.
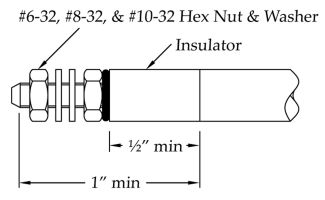
TYPE L TERMINATION - Screw lug terminal.
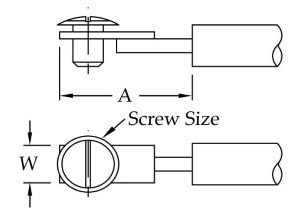
Screw Size |
Diameter |
A |
W |
#8-32 |
To 0.315" |
7/8" |
5/16" |
#10-32 |
0.375" and above |
1 1/16" |
7/16" |
Maximum 240V |
TYPE L1 TERMINATION - Screw lug terminal 90°.
Screw Size |
Diameter |
A |
W |
#8-32 |
To 0.315" |
7/8" |
5/16" |
#10-32 |
0.375" and above |
1 1/16" |
7/16" |
Maximum 240V |
TYPE D TERMINATION - Quick connect. Maximum 240V
TYPE D1 TERMINATION - Quick connect 90°. Maximum 240V
TYPE W TERMINATION - Leadwire terminal assembly.
Type |
Insulation |
Max. Temperature |
Volts |
WS |
Silicone |
390°F (200°C) |
600V |
WF |
Fiberglass |
480°F (250°C) |
600V |
WM |
Mica/Glass |
840°F (450°C) |
600V |
Note: If protective armor cable (hose) is required, please consult factory.
Seal Options for Tubular Heating Elements
TYPE G SEAL OPTION - Silicone Conformal Coating - General protection, porous, maximum temperature 220°F (105°C)
TYPE E SEAL OPTION - Epoxy Seal - Moisture and contamination resistant (better choice for long-term moisture resistance), low porosity, maximum temperature 450°F (230°C)
TYPE V SEAL OPTION - Silicone RTV - Moisture and contamination protection, porous, max. temperature 400°F (200°C)
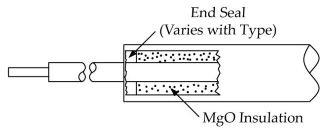
TYPE M SEAL OPTION - Silicone rubber over mold, max. temperature 300°F (150°F)
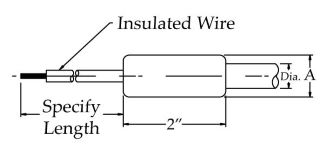
Diameter |
A |
0.260" |
7/16" |
0.315" |
7/16" |
0.430" |
5/8" |
TYPE PA SEAL OPTION - Potted adapter
Potted protection tube ensures an integral bond between wire insulation, the seal, and protective sleeving that may be required.
Type PS is silicone RTV and silicone insulated lead wireType PP is epoxy coating and Fiberglass insulated lead wireType PT is epoxy coating and Teflon® insulated lead wire
TYPE HS SEAL OPTION - Ceramic to metal hermetic terminals, max. temperature 1000°F (540°C)
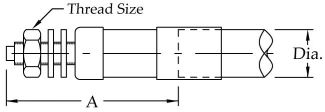
Thread Size |
Diameter |
W |
#8-32 |
0.260" |
1 3/4" |
#10-32 |
0.315" |
1 7/8" |
#1/4-28 |
0.430" |
2 1/8" |
Tubular Heater Construction Options for Tubular Heating Elements
Unheated Length - The unheated length can be varied to suit application requirements. Longer unheated sections are often used to keep the termination area cool or to focus heat generation in a specific area of the part or media being heated.
Distributed Wattage - Durex tubular heaters can be tailor-made to vary the watt density along the length of the heater. This aids in temperature uniformity in-mold applications or to make up for heat losses close to the ends.
Sheath Treatment and Finish - For tubular heaters that will be field bent, please be sure to specify "full anneal" on the order. For pharmaceutical and other "clean" applications, a bright anneal finish can be supplied. Also available, depending on configuration, is sheath passivation which removes any free iron that may stain or rust the finish of the sheath.
Tubular Heater Bending Options
Tubular heating elements can be formed into 2-D and 3-D shapes to better suit application requirements. Ensure to allow for up to 10% dimensional increase due to thermal expansion and to provide adequate support to prevent heating element sagging due to high temperatures. If field bending of straight elements is necessary, contact Durex Industries for field bending guidelines prior to bending. Also, specify "full sheath anneal" to allow for field bending.
Bend Tolerances for Incoloy® and Stainless Steel Sheath Elements
Bend Data Reference |
Heater Diameter |
|
0.260" |
0.315" |
0.375" |
0.430" |
0.475" |
0.490" |
Minimum Bend Radius Standard |
0.437" |
0.562" |
0.687" |
0.75" |
0.812" |
0.875" |
Minimum Bend Radius w/Repressed Bend |
0.375" |
0.50" |
0.562" |
0.625" |
0.687" |
0.75" |
Standard Bend Tolerances |
1/8" |
1/8" |
1/8" |
1/8" |
1/8" |
1/8" |
Special Bend Tolerances |
1/16" |
1/16" |
1/16" |
1/16" |
1/16" |
1/16" |
Precision Bend Tolerances w/Tooling |
0.005" |
0.005" |
0.005" |
0.005" |
0.005" |
0.005" |
Note: Tighter bend radii possible for steel and copper sheath elements. Please consult Durex Industries for more information.
Tubular Heating Elements Application Guidelines
Back to TopHeating Metal Parts
Below are the installation methods for heating metals in order of best to least effective.
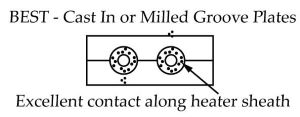
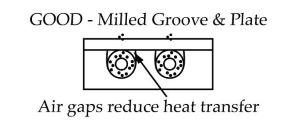
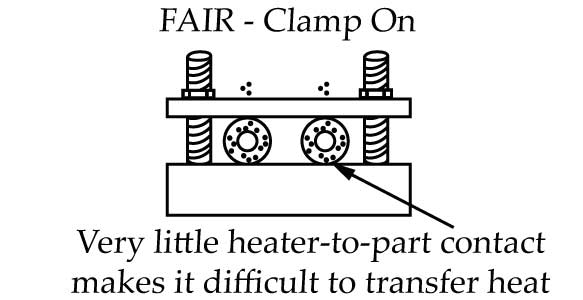
Durex Industries recommends to "press fit" the tubular heating element into milled groove plates for extended heater life. Ensure that all heated portions of the heater are in contact with the part. Heat transfer cement should be used to promote heat transfer. If clamps are used, they should be closely spaced and not over tightened to ensure good heater-to-part contact. Allow for up to 10% length increase due to thermal expansion during heating.
Heating Liquids
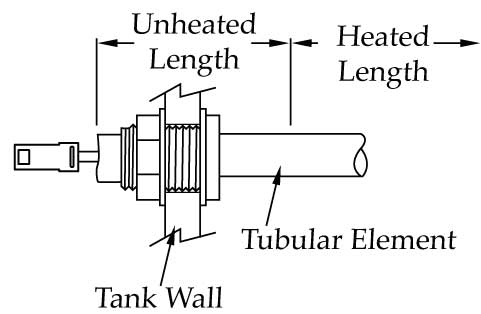
To prevent overheating or fouling the heating element, ensure the heated portion of the tubular heater is immersed in liquids AT ALL TIMES. For optimal results, properly match the sheath material and heater watt density to the liquid application. Factory installed fittings or field installed compression fittings are used to mount and seal the tubular element against the tank wall. Refer to the Immersion, Circulation, and Over-The-Side Heater sections of our website or catalog for other liquid heating products.
Heating Air & Gases
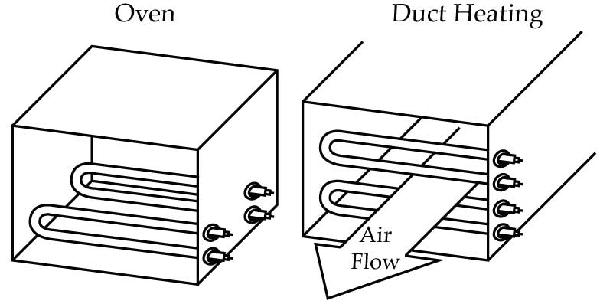
Tubular heating elements are typically formed into a "U" hairpin or other formation, installed through wall openings and secured with lock washers, clips, threaded fittings, mounting bracket or flange. For optimal results, use an Incoloy® sheath and ensure reasonable watt densities are used. Allow for 10% length increase due to thermal expansion. For horizontal installations, provide supports at least every 18" of length to avoid element sagging due to high temperatures. Refer to the Circulation and Duct Heater sections of the website or catalog for forced air and gas heating.
Radiant Heating and Vacuums
Tubular heaters used for radiant heating typically use reflectors to direct heat energy toward the part being heated. This works well for warming, drying, and curing applications. However, when using heaters in a vacuum, the only heat transfer is through radiation, so reduce watt density by 20% to 30% versus air heating. Aluminum sheath, as well as Inconel® sheathed heaters are typically used with vacuum feedthrough assemblies. Durex Industries can test and measure vacuum leakage rates down to 8x10-8 SCCS He (3x10-6 Pa 1/s).